Double Column Machining Centres and 5 Sided Machining
Double Column CNC Machining Centre
As its name suggests, a double column CNC machining centre incorporates two columns, with the spindle (the part of the machine where the cutting tool is mounted) moving between them. The double column design provides robust support for the spindle, allowing it to handle larger, heavier workpieces. It’s especially effective in reducing the vibrations during high-speed machining, contributing to more accurate, high-quality cuts.


Kafo double column machining centre
Structure and Components
The double column CNC machining centre typically includes a base, two vertical columns, a top beam (cross rail), and a work table. The base of the machine provides stability and firm footing. The two vertical columns are fixed onto the base. These columns provide support for the cross rail that houses the cutting spindle.
The work table is designed to hold large, heavy workpieces securely. Often, it includes a rotary table or pallet system to allow the machining of multiple faces of a part in one setup. The cutting spindle, housed in the cross rail, moves longitudinally (X-axis), vertically (Z-axis), and perpendicularly (Y-axis) to the X and Z axes.
Click here to see a time lapse of a Kafo double column to better understand its construction.
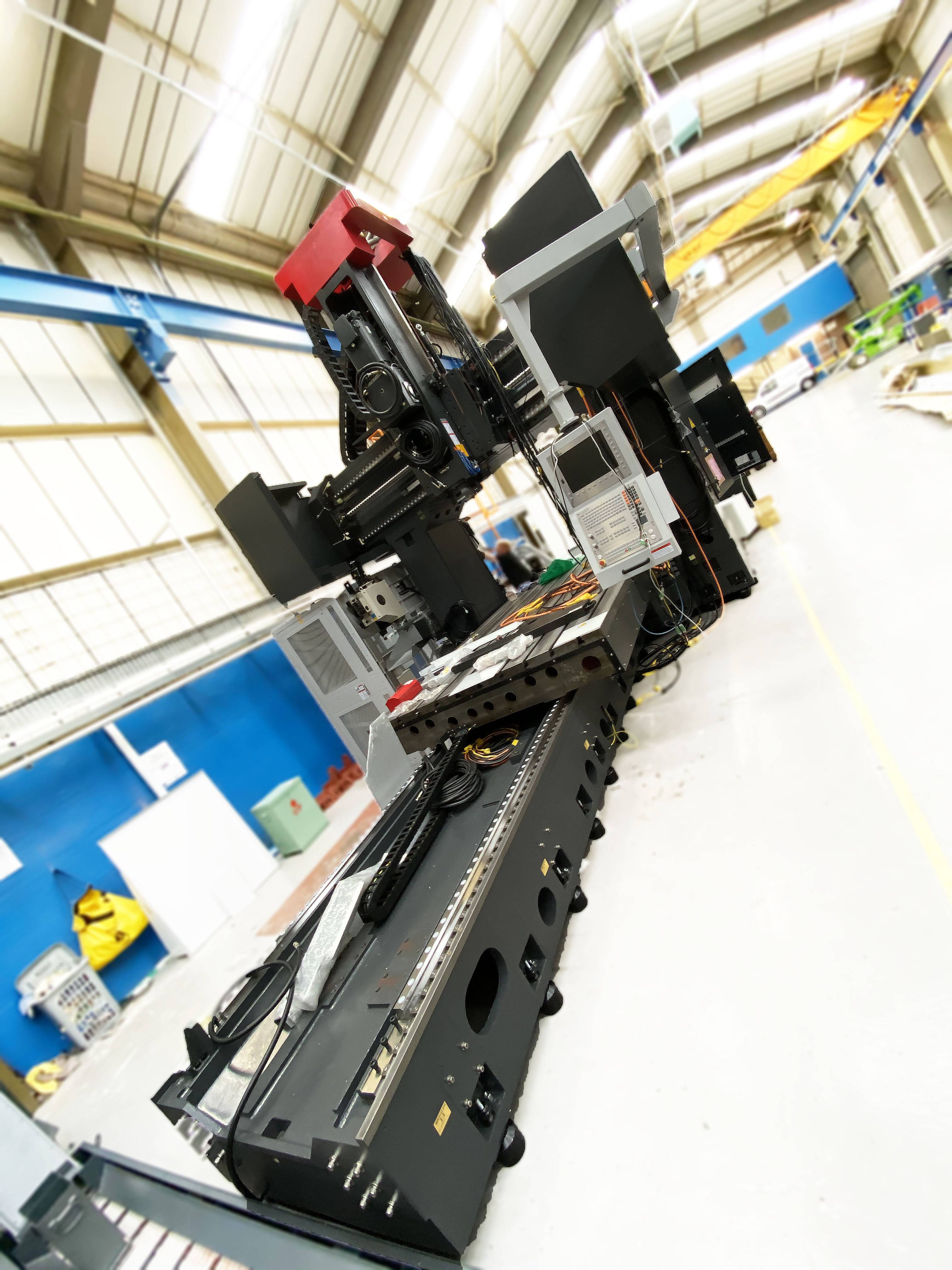
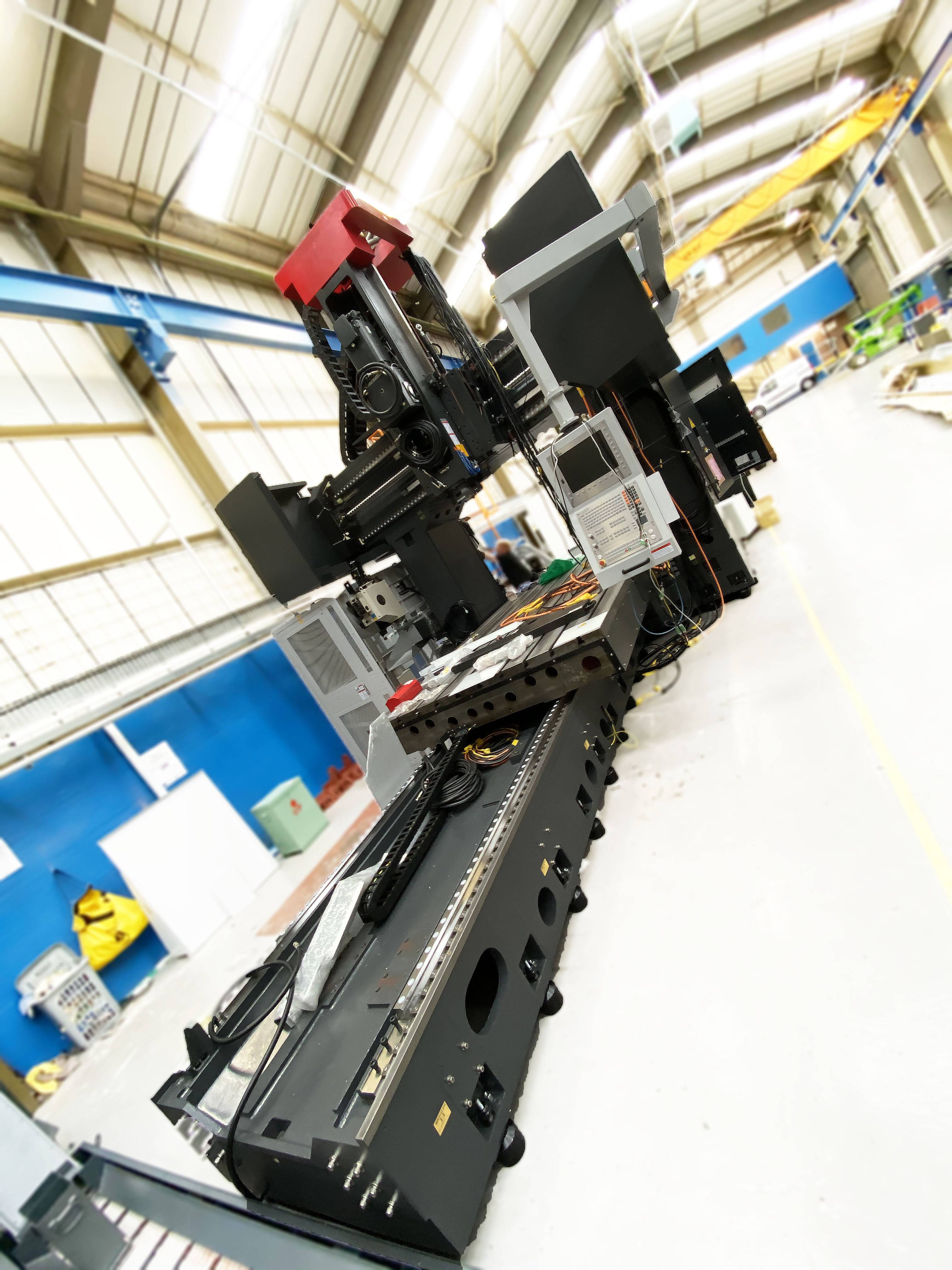
Kafo BMC-4122 Double Column – TDT CNC
Key Features and Benefits
Increased Stability and Rigidity: The double column configuration offers superior stability and rigidity, which is essential for maintaining accuracy during machining. It reduces vibrations and maintains a high level of precision even during high-speed machining or when dealing with hard materials.
Large Work Envelope: The double column design allows a large work envelope or machining area. It can accommodate large and heavy workpieces, making it suitable for industries such as aerospace, automotive, and energy where large part production is often required.
Versatility: With the right attachments and tooling, double column machines can perform a wide range of tasks including milling, drilling, tapping, and sometimes even turning.
Efficiency: Due to their stability and precision, these machines often produce high-quality parts with fewer passes, reducing waste and increasing efficiency.
Applications
In terms of application, these machines are commonly used where larger components need to be machined to high accuracy. This includes the aerospace industry (for aircraft parts), the automotive industry (for car parts), mould and die industry (for large moulds), and the energy sector (for turbine parts).
Limitations
While double column CNC machining centres offer many advantages, they are not without limitations. The primary one is their size. Due to their large footprint, these machines require a significant amount of floor space, which may not be feasible for smaller operations. In addition, the cost of these machines can be substantial, making them a substantial investment.
Conclusion
The double column CNC machining centre embodies the fusion of modern technology and traditional manufacturing processes, offering precision and versatility in machining large workpieces. Despite their size and cost, they are an indispensable tool in industries where accuracy and efficiency are paramount. Their use continues to evolve with advancements in technology, ensuring their ongoing relevance in modern manufacturing.
For more information on Kafo double column machining centres, click here
Five-Sided Machining on a Double Column Machining Centre
Five-sided machining, also known as 5-axis machining or pentahedron machining, is a cutting-edge manufacturing process that employs CNC technology to move a part or a cutting tool on five different axes simultaneously. This capability enables the machining of very complex parts, which is crucial in advanced industries such as aerospace, automotive, medical, and energy. Double Column Machining Centres can be fitted with 5-axis capabilities, effectively enhancing their machining possibilities. The five-sided machining process on these machines provides a series of significant advantages, including precision, flexibility, and time efficiency.


Hitting 5 sides – 5 sided machining
1. Understanding Five-Sided Machining:
The term “five-sided machining” refers to the ability of a machine tool to move a cutting tool or a workpiece in five different planes or directions simultaneously. This involves three linear axes (X, Y, and Z) and two rotary axes. The combination of these movements allows the cutting tool to approach the workpiece from any direction.
In the context of a double column machining centre, this would typically involve a 3-axis movement of X, Y and Z then 2 axis movement of the cutting tool using 90 degree or universal heads.
KAFO, 90 degree Universal Milling head
2. Key Features and Benefits:
Complex Machining Capability: Five-sided machining allows for the machining of complex geometries that would otherwise be difficult or impossible to achieve. By enabling the tool to approach the workpiece from any direction, complex and intricate parts can be manufactured in a single setup.
Increased Precision and Accuracy: This method reduces the number of setups, thereby minimizing the potential for error. Each time a part is repositioned for a new machining operation, there’s a risk of misalignment. By completing multiple operations in one setup, five-sided machining improves accuracy.
Efficiency and Time-Savings: The reduction in setups also translates to less time spent preparing the workpiece and more time actually machining. This boosts productivity, decreases lead time, and reduces costs.
3. Five-Sided Machining Process:
To accomplish five-sided machining on a double column machining centre, the process typically begins with the creation of a CAD (Computer-Aided Design) model of the part to be produced. This model is then converted into a CNC program using CAM (Computer-Aided Manufacturing) software, which includes the specific instructions for the tool paths.
The workpiece is then securely mounted on the work table, typically a rotary table, which allows for rotation and tilting of the workpiece. The CNC program is loaded into the machine’s control system, and the machining process begins. The cutting tool moves in the X, Y, and Z directions, while the rotary head manoeuvres the spindle in a manner that allows the tool to access it from all sides.
4. Applications:
Five-sided machining on a double column machining centre is particularly advantageous in industries that require the production of complex parts, such as aerospace, automotive, medical, and die and mould manufacturing. For instance, it can be used for the efficient production of engine parts, turbine components, orthopedic implants, and intricate moulds.
5. Considerations and Challenges:
While five-sided machining provides numerous benefits, it also requires a higher level of skill and understanding to operate effectively. Programming for 5-axis machining is more complex and requires skilled operators and programmers. Moreover, initial setup and equipment costs can be high, particularly for high-quality CNC machines and associated software.
Conclusion:
Five-sided machining on a double column machining centre is a powerful technique that greatly expands the potential of CNC machining. By allowing the machining of complex parts in a single setup, it offers significant benefits in terms of precision, flexibility, and efficiency.